How Are Challenge Coins Made?
The Custom Coin Minting Process
A Closer Look at the Coin Production Process
We get a lot of questions about how we make custom challenge coins, so we decided to give you a behind the scenes look at our challenge coin production process. We’ll break down all the big steps in the coin manufacturing process, so you can see exactly how your challenge coins are made from start to finish.
We’ll be picking up the process right when our production team sets to work on a finished coin design. You can learn more about how to design a challenge coin in our challenge coin design 101 video. For now, let’s move on to the first step in coin production.
Step One: Making a Custom Coin Mold
The first thing we need to do is create a challenge coin mold, and the process of making a custom coin mold starts with a computer called a CAD.
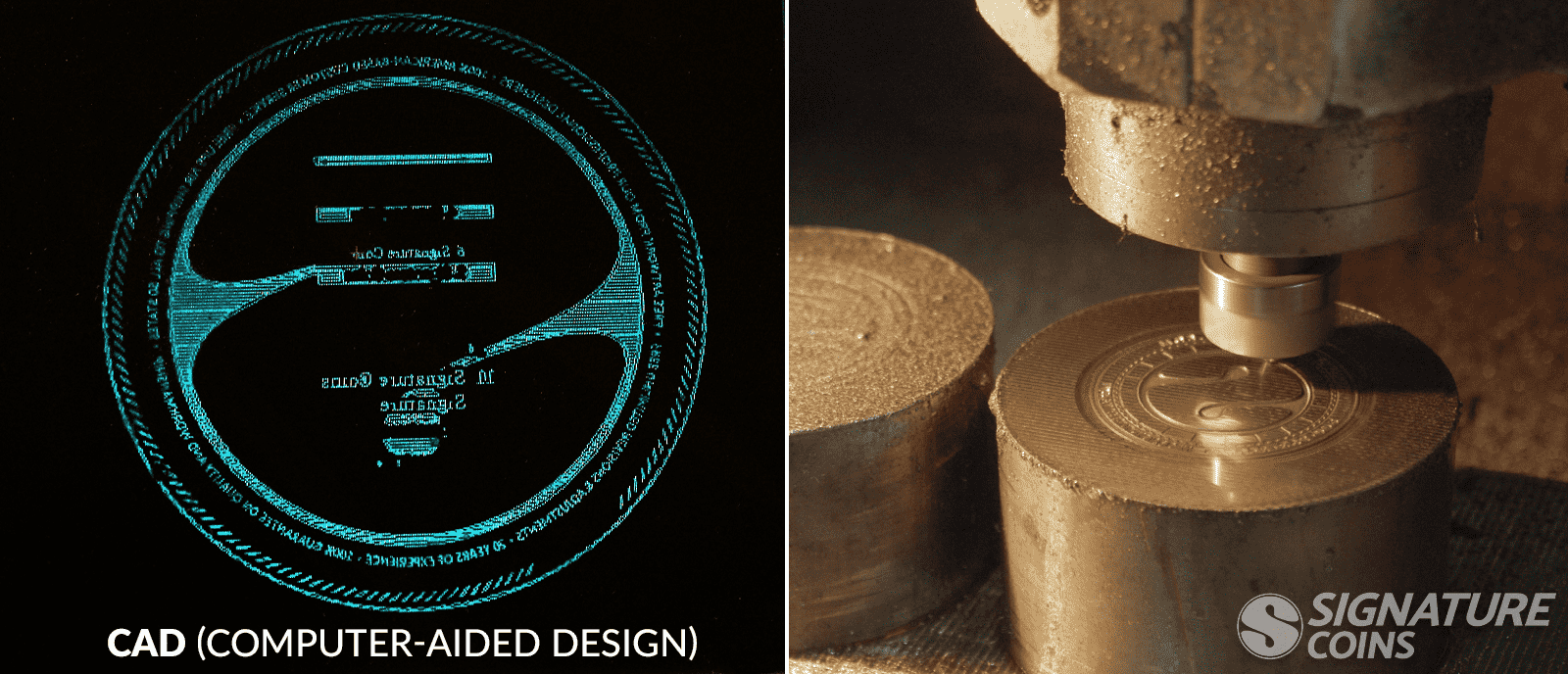
A CAD, or Computer-Aided Design, is a computer program that uses the custom artwork of a coin to create a digital blueprint of the design that we can use for manufacturing. The CAD maps out the tolerances and dimensions of the coin, accounting for the materials we will use, and we upload all of this information into another computer called a CAM (Computer-Aided Manufacturing) software.
The CAM runs a CNC, which is essentially a computer-controlled mill. In the coin production process, milling involves using a cutting tool to progressively remove material from the surface of a steel block, cutting the inverse of a coin design into the metal.
This is how we make custom coin molds. One mold is cut for the front of the coins, and one is cut for the back of the coins. Once the CNC is finished cutting the steel coin molds, we test them by striking soft pieces of metal and examining the impressions they make. If we see any imperfections in the design, we can make adjustments to the molds before moving forward.
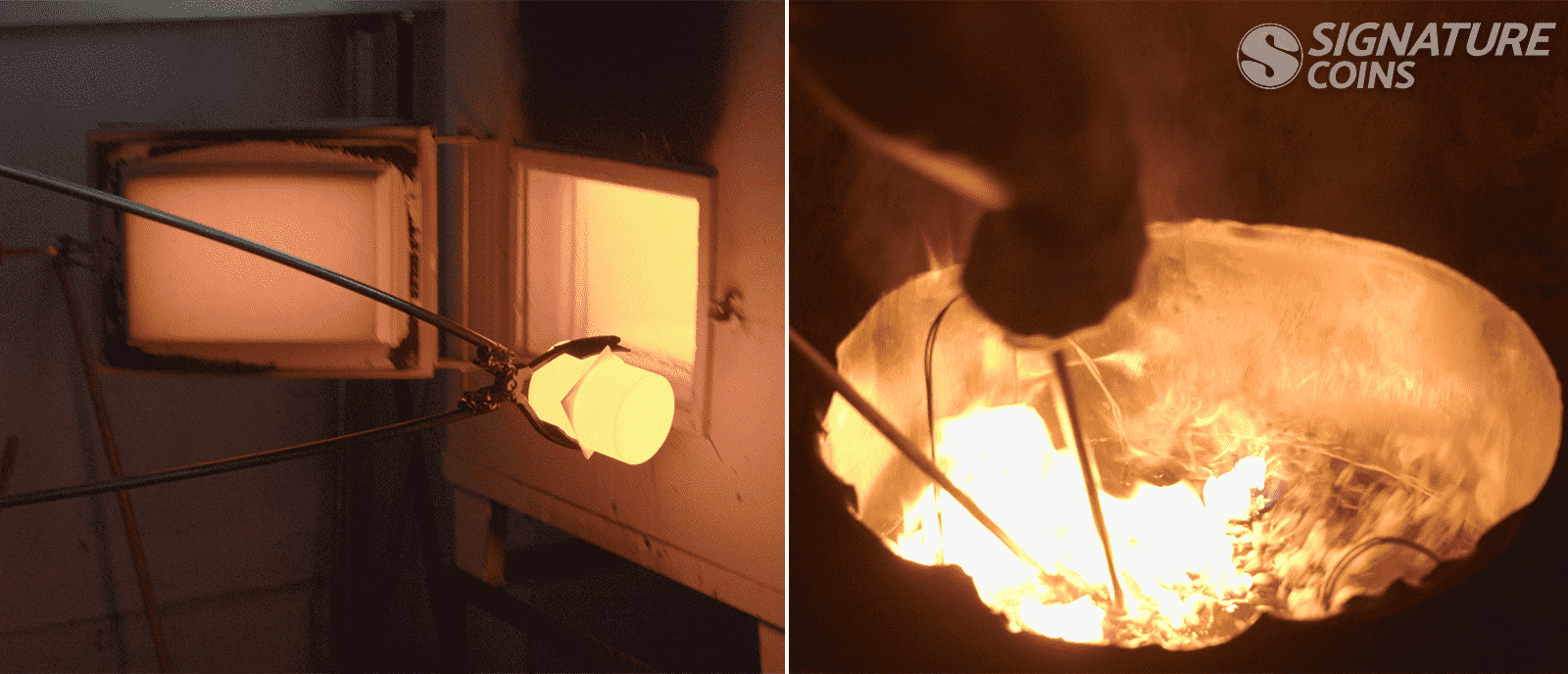
Once we’re satisfied with the molds, we temper them in a hot oven. This hardens the steel, making it tougher and better able to stand up to the immense force of die striking brass coins. Once the molds are red hot, we take them out of the oven and douse them in cool oil. It takes anywhere from 500 to 1,000 tons of force to stamp a design into brass, and heat-treating the coin molds beforehand ensures that they are up for the task.
Step Two: Die Striking Challenge Coins
Coin molds are sometimes called dies, which is where the term die striking comes from. Die striking involves using the freshly made coin molds to stamp artwork into brass. It sounds pretty straight forward, but depending on the type of coins being made, die striking can look a little different.
Round coins, for example, are usually made from coin blanks. As it sounds, coin blanks are just featureless round medallions that have been removed from a strip of brass. Once we fit the coin molds to a coin press, we place the coin blanks between the molds and use the coin press to stamp the molds against the blank coins.
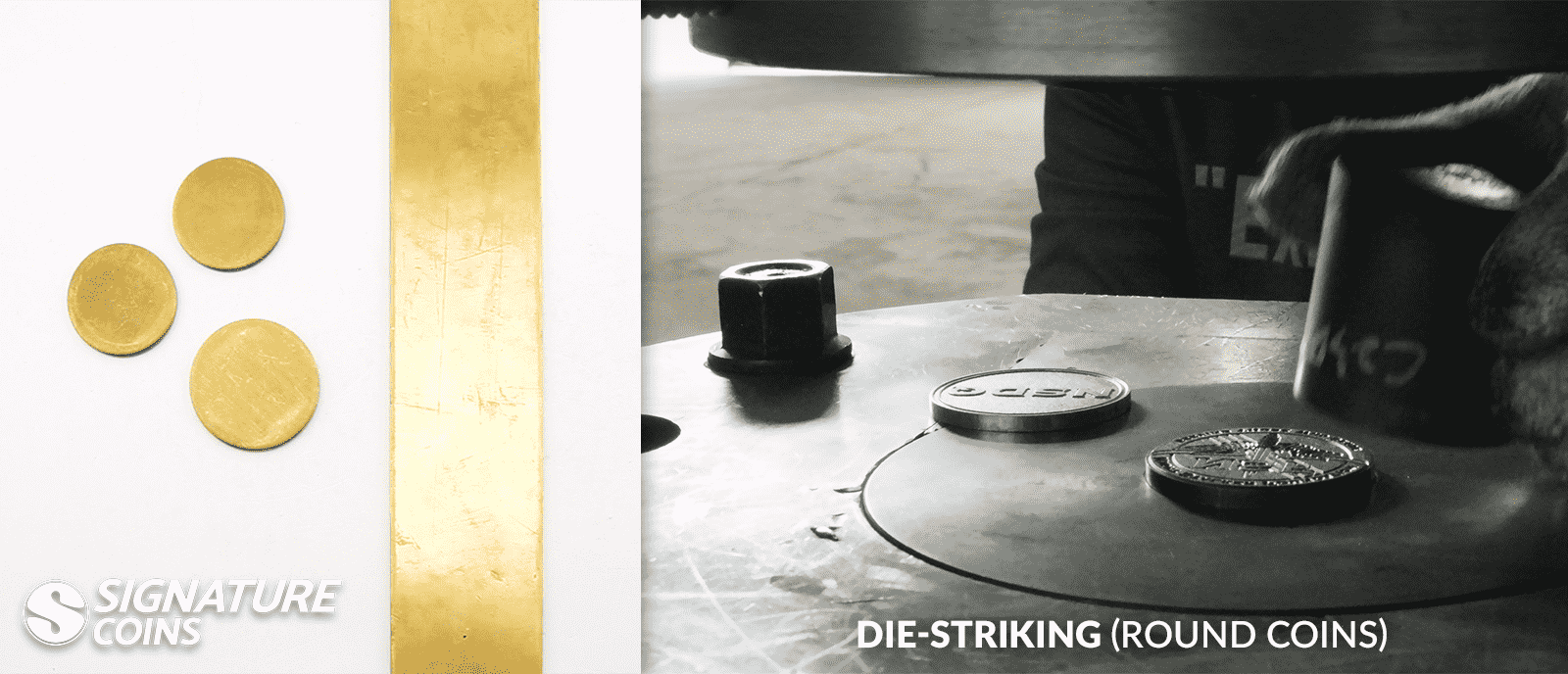
We create coin blanks by feeding strips of brass or steel through a coin press fitted with a round cutting tool. When the coin press comes down, the round coin blanks are cut free and collected for die striking later on. Finished challenge coins are 1.5” to 2” in size on average, so these are the typical sizes we adhere to for coin blanks.
However, we don’t always use coin blanks during the die striking process. Things look a little different for custom shaped coins. Instead of feeding a brass strip through a coin press and cutting out round coin blanks, we just stamp multiple impressions of the coin design along the entire length of the brass strip and cut them out once the die striking process is finished.
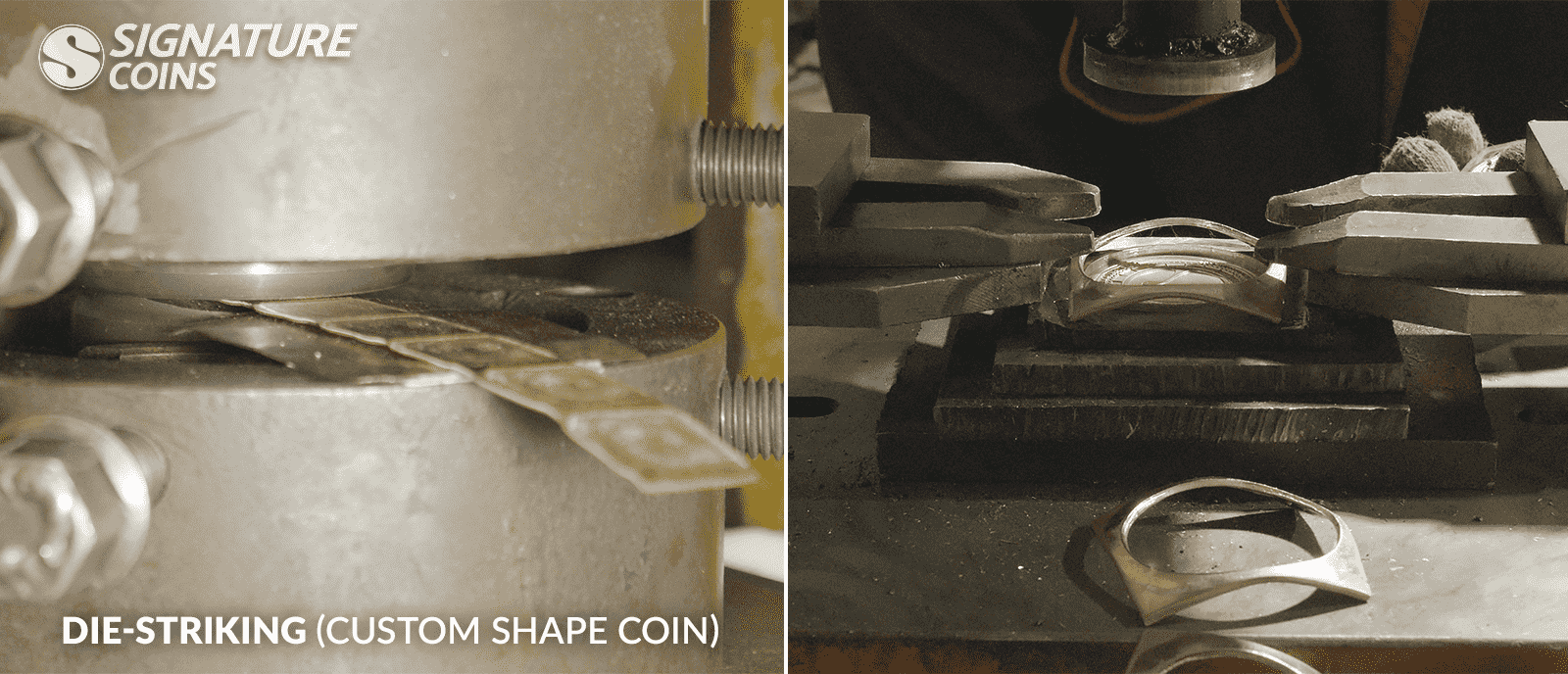
Since the coins are custom shaped, we need a custom shaped cutter to remove them from the brass strip. We create a cutter through a Wire EDM process. It’s used on everything from circular coins to the most complex shapes you can think of.
Just like the coin molds, the cutting molds need to be trimmed and heat-treated before use. When it’s ready, we load the cutting mold into a special coin press, and when this press comes down on the brass strips of metal, the coins are cut free with the impressions of the artwork already in place.
Step Three: Cutting the Edge and Deburring the Coins
No matter how the die striking process looks, stamping and cutting metal creates sharp ridges and spurs across the entire surface of the coins. Handling them without gloves at this point can be a little dicey, so we need to deburr them before moving on.
However, depending on the edge you choose for your design, there may be an extra step between die striking and deburring. This is because some edges are hand-cut.
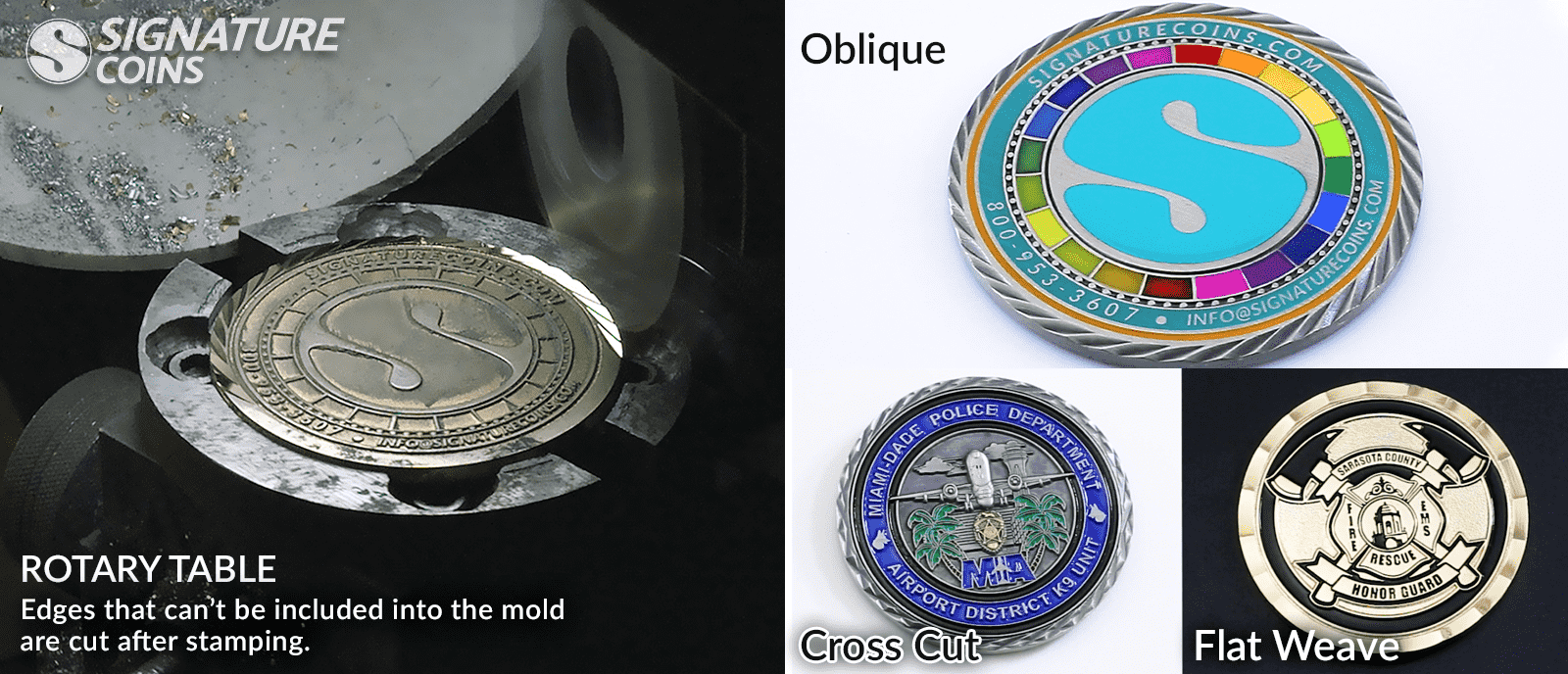
We do this by loading the coins into a rotary table and cutting the intricate pattern along the edge of the coins by hand as the table spins. The coins are finished individually, and once they’re all finished, we put them all through the deburring process.
Deburring is done in a few different ways. Sometimes, coins are tumbled in dry media, and other times, they’re put into a machine with water, soap, and porous stone that will rub against the coins as the machine spins.
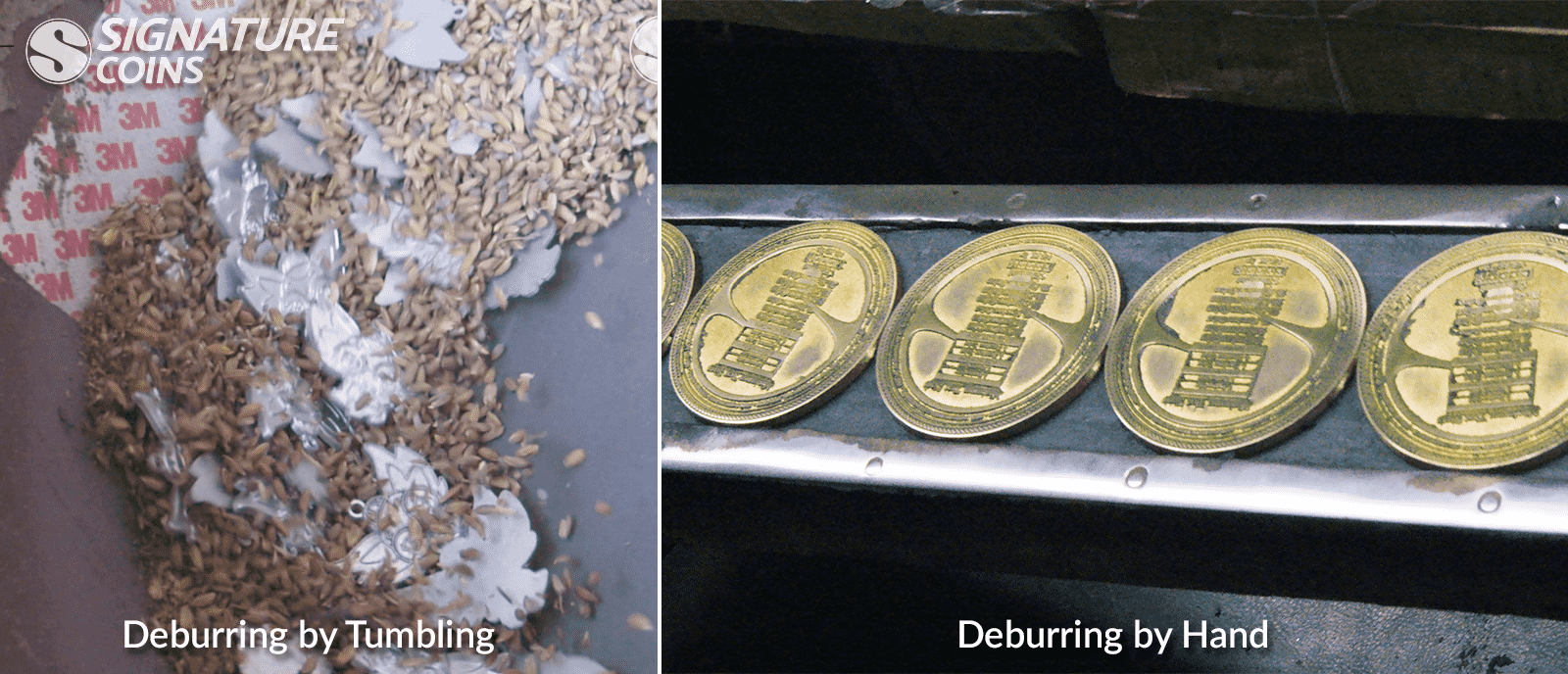
We also deburr coins by hand. We line them up on a wooden block and hold the block against a spinning wheel to smooth the surface of the coins. No matter which deburring method our production team chooses, the end result at this point is a set of coins that have a smooth, polished texture.
Step Four: Custom Metal Plating and Colorfilling
Depending on the type of challenge coin, these last elements of challenge coin minting can happen in a different order. Soft enamel coins go through the custom metal plating process first and then go through colorfilling. Hard enamel coins go through colorfilling first and then go through metal plating.
Soft enamel is the most common type of custom challenge coin, so we’ll walk you through that process first.
Freshly deburred coins are collected and hung from copper wire. This plays a big part in the metal plating, or electroplating, process. Electroplating is mostly a chemical process. We take the coins hung from the copper wire and dip them into troughs full of water.
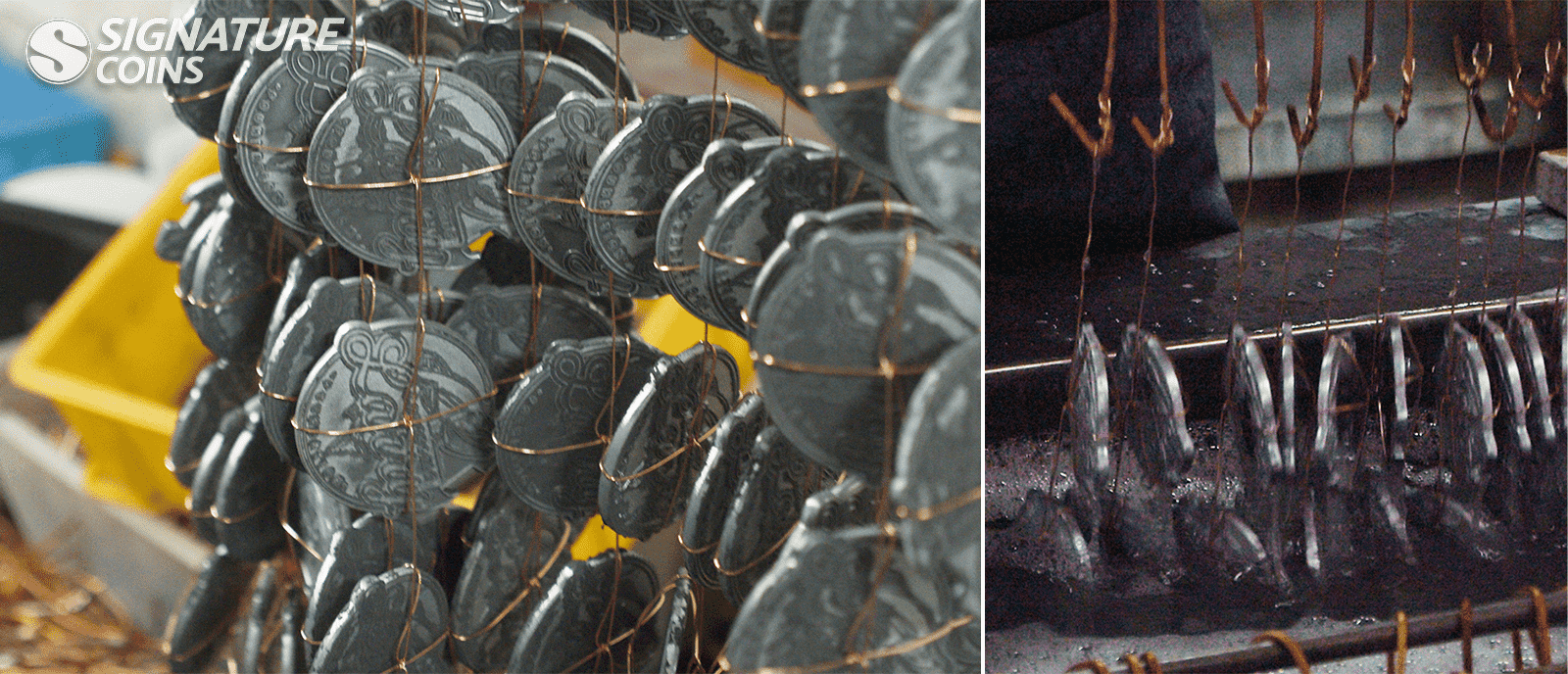
They’re first dipped into clean water and then into different chemical solutions to clean the surface of all of the coins. This ensures that the coins receive an even layer of metal plating. The actual metal plating process happens when we soak the coins in a solution containing the precious metal chosen to cover the design.
We usually plate coins in gold, silver, or copper, but we also make black nickel coins and rainbow metal coins. No matter the case, an electrical current is run through the solution containing the coins and the precious metal. The coins, grounded by the copper wire, attract the precious metal to form a thin, permanent layer of custom metal plating.
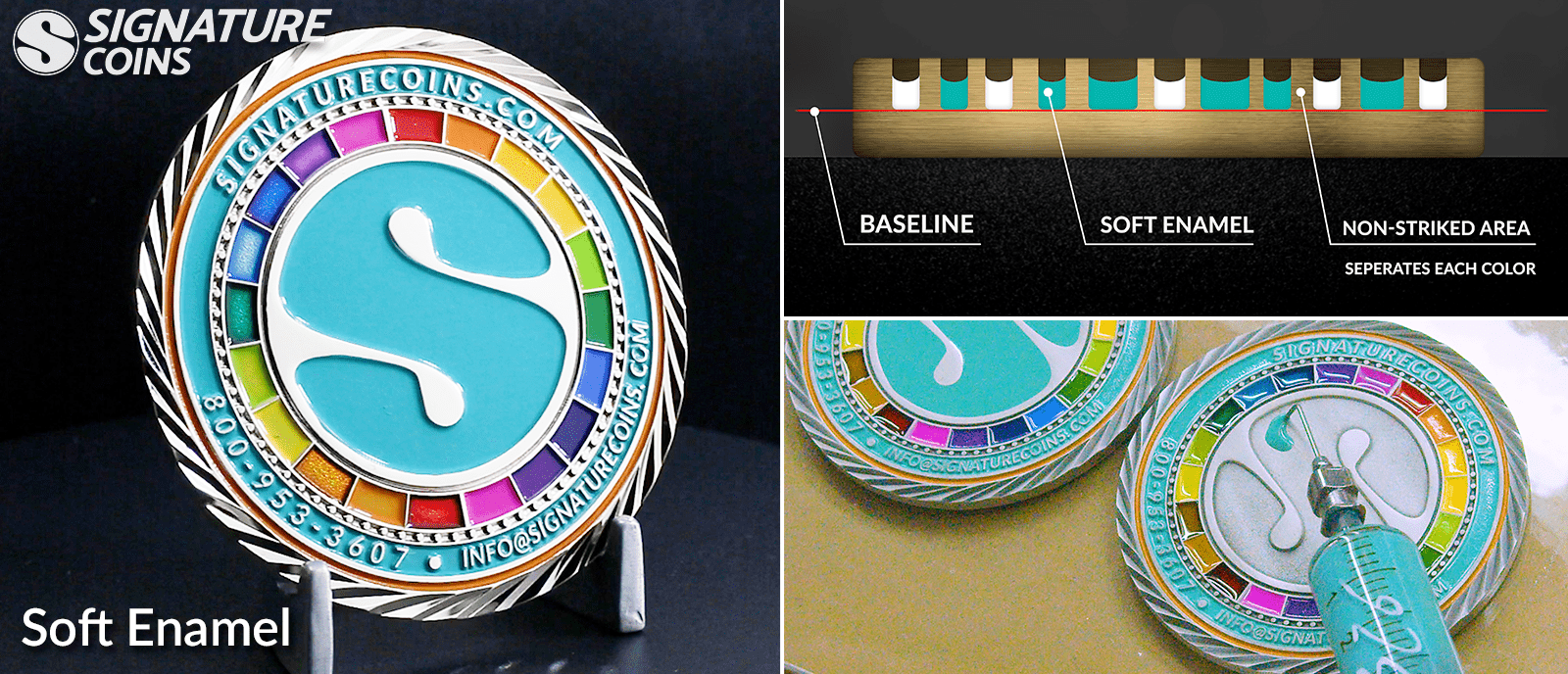
After the coins are removed and dried, they go to the colorfilling room. Colorfilling is usually done by hand, but we also have machines that automate the entire process. For orders of about 100 coins, it’s faster to do it all by hand.
Members of our production team use special syringes full of soft enamel paint to fill in the recessed areas of the design. Once all of the colors have been added, we put all of the coins into an oven to let the enamel cure.
At this point, soft enamel challenge coins are just about finished, but remember when we said that hard enamel coins go through colorfilling before metal plating? There’s a good reason for this.
Hard enamel coins have a smooth texture because the enamel paint is at an even level as the raised metal strokes of the design. Soft enamel coins have a more layered appearance because the enamel paint is all contained within the recessed portions of the artwork, using the raised metal strokes to separate colorfill areas.
So, the colorfill areas on a hard enamel coin are actually overfilled, unlike soft enamel coins which only need a small amount of paint to reside in the recessed area.
The recessed areas of a hard enamel coin that need color are overfilled with enamel paint, and then the coins are placed in an oven to let the paint cure. This process is repeated for every color. Once all of the colors have cured, the coins are polished by hand.
The polishing process grinds away the excess enamel paint so that the surface of the coins has a crisp, even appearance.
When it comes to metal plating, the only difference between hard and soft enamel coins is that hard enamel coins already have all of their enamel colors in place before going through the plating process.
Step Five: Laser Engraving and Quality Control
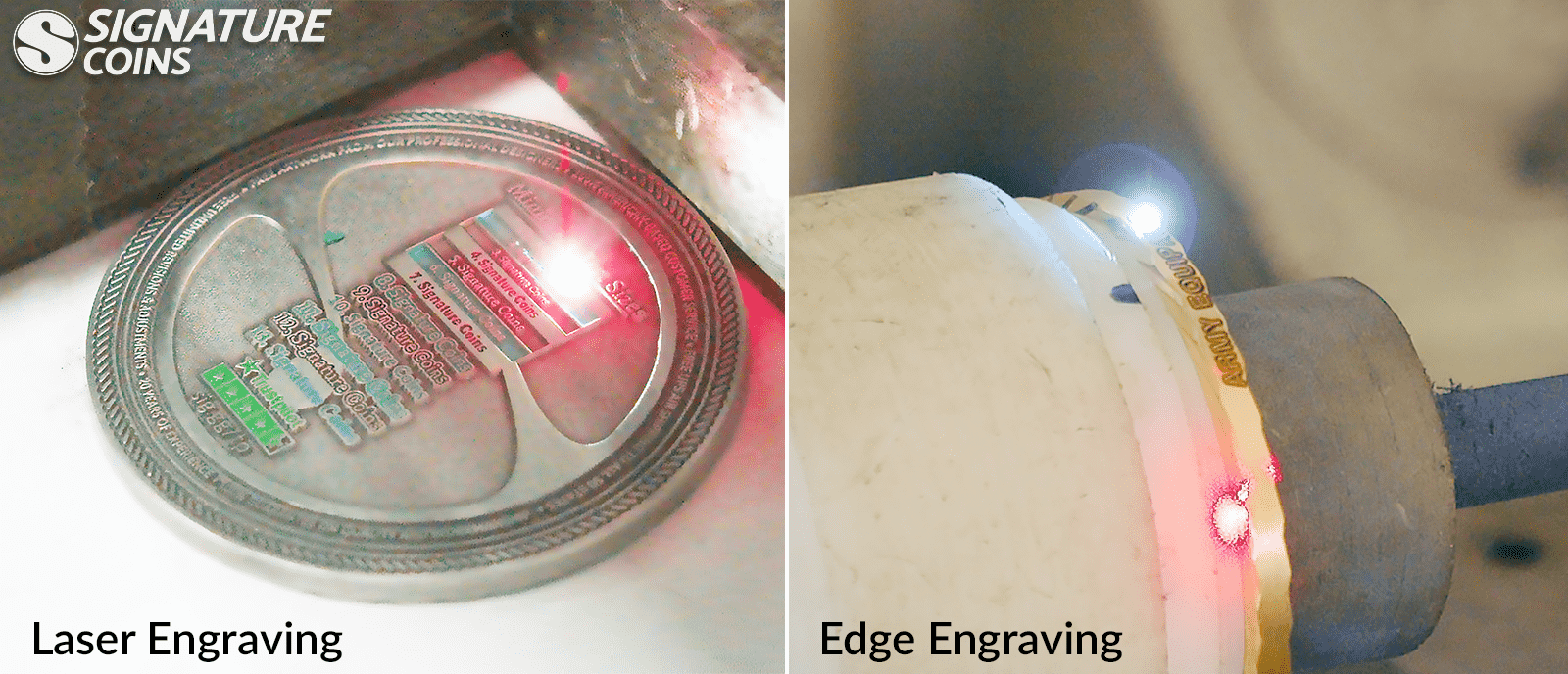
At this point, the coins are almost finished. Depending on the design, the last step in production is laser engraving. We use laser engraving to include small details that are not possible to create using the die striking method.
We can laser engrave different names onto the surface of a coin or along the true edge of a coin. We also use laser engraving to include sequential numbering on a series of coins. It all depends on what the design calls for.
Once laser engraving is finished, if it’s needed, the last part of the challenge coin production process is quality control and packaging.
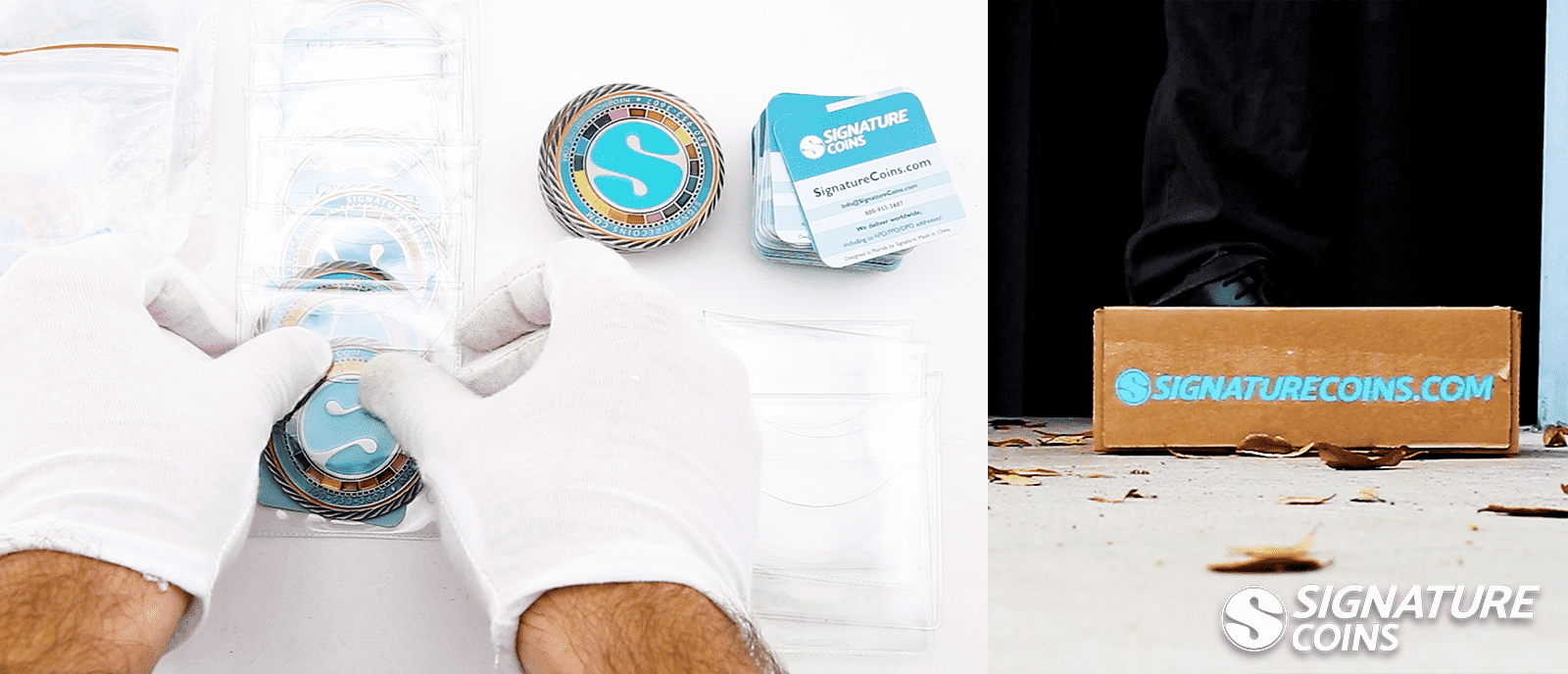
All of the coins are inspected and prepared for shipping. In the rare occasions when we find coins that do not meet our quality standards, we set them aside and create new ones so we can fill the order.
And that’s that! The coins are shipped via UPS or FedEx priority air shipping and arrive at their destination within two days of leaving our production team.
High-Quality Challenge Coins From the Best Custom Coin Maker Online
Making high-quality custom coins is what we do. Our Signature Coins team has been handcrafting challenge coins since the year 2000, and we knows all of the ins and outs of the challenge coin minting process.
We’ll help you create a custom design, completely free of charge, and have your coins manufactured and delivered in 14 days or fewer. What kind of challenge coins would you have made? Give us a call and let us know! We take care of all the big stuff for you, so bringing your ideas to life is easier than you might think.